How Auto Gauging Improves Honing Accuracy and Efficiency on the Shop Floor
16 Jul, 2025
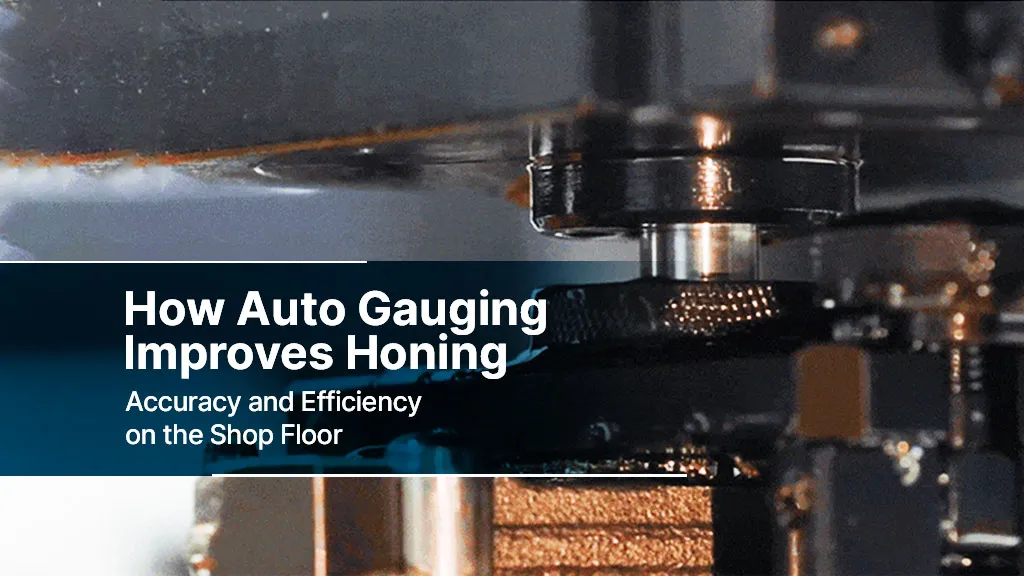
Nothing slows down your day like a part that doesn’t meet the spec or standard.
You’ve set everything up. The machine’s running fine. But then that one product comes out slightly oversized or just a little too tight. You’re back to checking, adjusting, maybe reworking.
And just like that, the whole batch ends up in scrap — time, material, and effort, all gone.
It might not seem like a big deal – after all, it’s just one part, right? But over time, those small misses stack up and form into real problems. Delays. Scrap. Customer complaints.
That’s why more manufacturers are turning to auto gauging. Not because it’s trendy. Not because someone in a tie said it’ll “redefine operations.” But because it actually solves the problem, quietly, reliably, and without needing to work on it again. Let’s walk through what it is, how it works, and why it’s become one of the most valuable upgrades you can get on the shop floor.
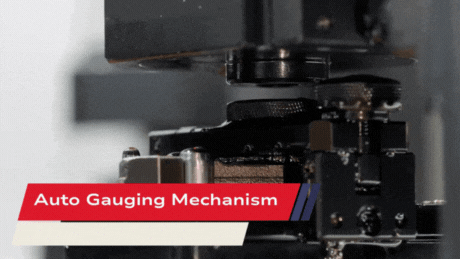
What Is Auto Gauging in Honing?
Auto gauging is the process where the honing machine measures the bore size of a component automatically during the machining cycle.
And if the bore shape or surface is even a little off, the machine adjusts as needed. No need to stop. No need to remove the part. No need for manual checks between steps.
It all happens inside the machine, while the part is still in position. What that really means is:
- Operators don’t have to check the size after every step
- There’s no need to stop the machine or remove the part
- And most importantly, the chances of sending out a non-compliant part go way down
Let’s take a situation as an example –
Let’s say you're working with ±0.003 mm tolerances. A single missed cut can turn into an entire batch being flagged or rejected.
Customers are demanding tighter tolerances. Volumes are going up. And downtime? That’s the one thing nobody can afford.
Auto gauging gives you control in the one place that matters most, the point of machining.
Why Auto Gauging Makes a Difference on the Shop Floor
Now, not every shop needs this.
If you’re only running a few parts a day and your tolerance limits are wide, you might not notice much difference.
But if you're working with large batches and parts that need tight size control – like in automotive, aerospace, defence, marine, or hydraulic systems, then this small feature can have a big impact.
Here’s what we’ve seen it improve directly on the floor:
- No back-and-forth handling – The part stays in the machine. It checks itself. You don’t need to move it around just to measure.
- Less scrap – When the bore is measured inside the machine, you catch mistakes early. That means fewer parts go to waste.
- No last-minute surprises – The machine tells you if the part is within spec before it even comes out. So you’re not finding issues after the job’s done.
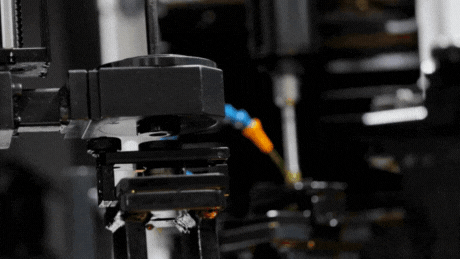
How Manufacturers Are Adopting Auto Gauging in Honing
Just a few years back, honing machines were a premium add-on that most plants rarely used.
But today, many honing machine manufacturers are either offering it as standard or as an upgrade, because more customers are demanding it.
And it makes sense. These days, precision matters just as much as speed, sometimes even more than cost. When your job depends on tight tolerances and fast turnaround, it helps to have a system that double-checks things for you in real time.
In high-volume setups, even a small improvement in bore accuracy can cut down rework and scrap. That’s where automated gauging shows its real value, by flagging issues before they cause bigger problems.
Who Actually Needs This?
If your work involves parts where bore size, geometry, and surface finish really matter, then auto gauging isn’t just useful, it’s a key part of keeping your quality and consistency on track.
Here are a few industries and components where it’s already being used, and where it makes a noticeable difference:
Automotive & EV Manufacturing
- Engine blocks
- Crankshaft bores
- Brake master cylinders
- Connecting rods
- Gear housings
- Fuel injectors
- Valve bodies
- Transmission casings
Aerospace
- Hydraulic actuators
- Landing gear cylinders
- Fuel system sleeves
- Engine bushings
- Control system parts
Hydraulics & Pneumatics
- Pump housings
- Cylinder barrels
- Spools and sleeves
- Valve blocks
- Pneumatic actuators
Railway Locomotives
- Traction motor housings
- Brake cylinder blocks
- Axle box parts
- Suspension dampers
- Transmission components
Defence & Military
- Gun barrels
- Missile system sleeves
- Engine blocks for defence vehicles
- Turret control cylinders
- Precision mounts and guide sleeves
Heavy Equipment & General Engineering
- Excavator pin bores
- Large engine casings
- Gearbox housings
- Bearing seats
- Compressor blocks
How Auto Gauging Works in a Real Production Line
Auto gauging brings real-time control to honing, helping the machines respond as they work, without having to wait for human input. Here’s how a six-station setup typically functions:
Loading & Unloading Station
- The operator loads the part manually or through automation.
- The system confirms the part is loaded and logs the details for traceability.
Input Gauging Station
- Before any machining, the bore is measured.
- The machine uses this info to calculate how much to remove during roughing.
- You can see the measurement and component status live on the HMI.
Roughing Station (Spindle 1)
- Based on the input measurement, the rough honing starts.
- Material is removed to get closer to the target size.
- The HMI logs how much was removed and confirms that the step is done.
Post-Roughing Gauge Station
- After roughing, the bore is checked again.
- If the size is on target, it moves to finishing.
- If not, the system adjusts the process for the next part automatically.
- Real-time values and feedback are shown on the HMI screen.
Finishing Station (Spindle 2)
- Final honing happens here, guided by the previous measurement.
- This is where the bore reaches its final size and surface finish.
- The HMI updates the process status and records the result.
Output Gauging Station
- This station checks the final bore size.
- If it’s within tolerance, the part is marked OK and unloaded.
- If it’s not, the machine triggers Auto Size Compensation and adjusts the next cycle automatically.
- The HMI clearly shows the result – “pass or fail”, and logs the feedback.
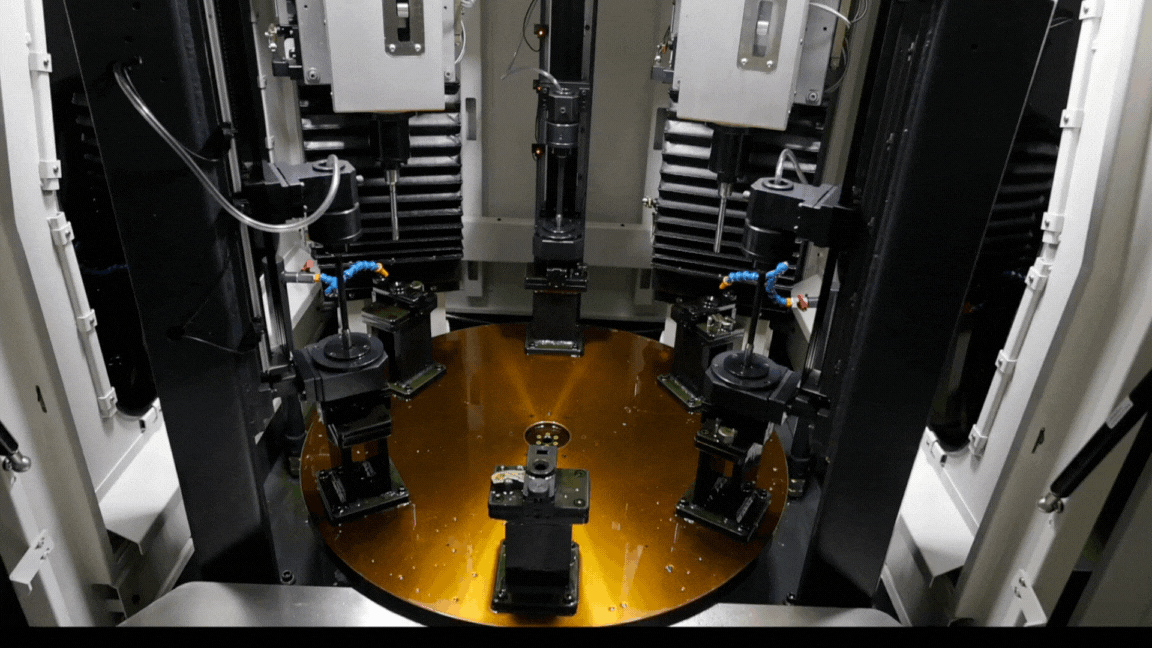
Real-Time Visibility Through the HMI
- Operators can monitor the full process in real time through the HMI — from the first bore measurement to the final pass.
- Each station displays its results, and any adjustments are logged instantly and clearly.
- If the input size of a part is out of the expected range, the system automatically stops the machine and alerts the operator.
This combination of live measurement and feedback removes the need for guesswork and reduces manual intervention. You get more control, better accuracy, and fewer reworks, right from your machining cell.
Why It Matters in Tight-Tolerance Industries
In sectors like aerospace, automotive, railways, marine, hydraulics, and pneumatics, tolerances leave very little room for error. That’s where auto gauging makes the biggest impact, helping catch and fix small deviations before they turn into bigger problems.
When you’re running hundreds of parts a day, this kind of automation helps your team work faster, more accurately, and with less stress.
Final Thought
Auto gauging isn’t just another quiet feature sitting in the background. It does exactly what it should — measuring, adjusting, and keeping things on track, without adding time, effort, or noise.
Whether you’re making EV motor parts, aircraft actuators, or hydraulic sleeves, auto gauging delivers everyday reliability where it matters most, right at the point of machining.
On the honing machines we’ve worked with at Abhi Fine Products, auto gauging doesn’t feel like an optional add-on anymore. It simply fits into the workflow.
If you’re thinking about your next upgrade, let’s talk – our team can help you decide if auto gauging is the right fit for your production line.
Tell us how can we assist you?
We are always happy to answer any questions!
Just fill in the form and we will get back to you.
© 2025 All rights reserved. Abhi Fine Products.
Designed & Developed by Appac Mediatech Pvt Ltd