Why Honing Fixtures Are Key to Consistent Surface Quality?
30 Apr, 2025
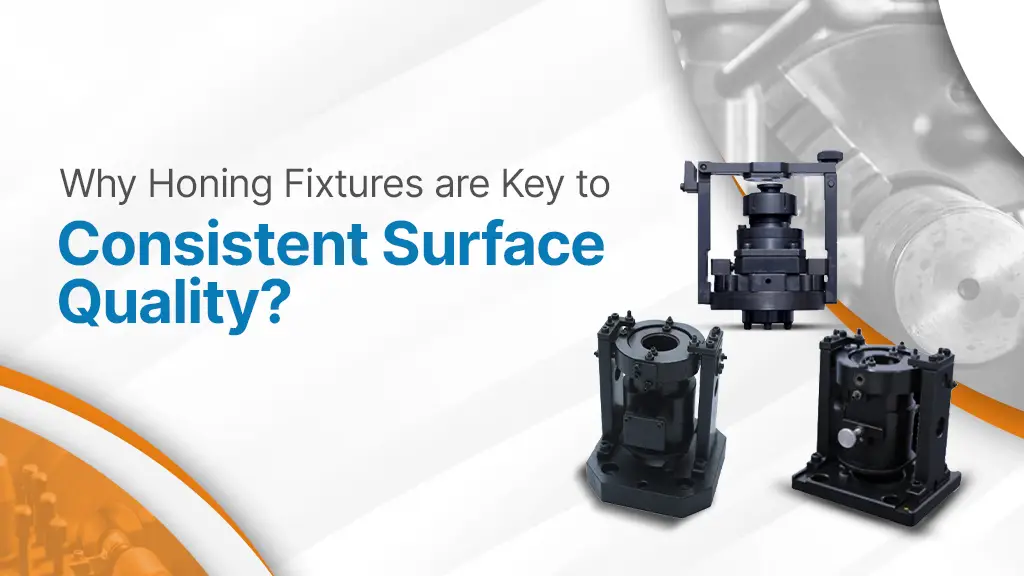
In precision machining, honing stands out as a critical process for improving surface quality, dimensional accuracy, and geometric perfection. While the honing machine itself is inevitable, the honing fixture is often the crucial one, ensuring consistent results. A honing fixture provides the necessary support and alignment for the workpiece during the honing process, allowing for greater control over surface finish and tolerance. In this blog, we’ll explore why honing fixtures are essential, how they work, and why they are critical for achieving consistent surface quality.
What is a Honing Fixture?
A honing fixture is a specialized holding device used to secure and position the workpiece during the honing process. It ensures that the workpiece remains stable and aligned, allowing the honing tool to make consistent and accurate contact with the surface. Without a proper fixture, even the most advanced honing machine may struggle to deliver a uniform finish.
Honing fixtures come in different types, depending on the shape, size, and material of the workpiece. They are designed to minimize vibration, maintain alignment, and provide the necessary pressure for a consistent honing action.
How Honing Fixtures Improve Surface Quality
1. Precise Alignment and Positioning
Honing fixtures ensure that the workpiece is correctly aligned with the honing tool. Misalignment can lead to uneven wear and poor surface finish. A well-designed fixture holds the workpiece firmly, preventing any lateral movement that could affect the honing path.
2. Reduced Vibration and Deflection
Vibration during the honing process can create micro-scratches and inconsistencies on the surface. Honing fixtures reduce vibration by securing the workpiece tightly and absorbing excess movement. This leads to a smoother, more uniform finish.
3.Consistent Material Removal
Proper fixture alignment ensures that the honing tool engages evenly with the surface, allowing for consistent material removal. This results in better surface texture and improved roundness, straightness, and cylindricity.
4.Better Control Over Tolerances
High-performance honing fixtures allow manufacturers to maintain tight tolerances. By controlling the positioning and pressure of the honing tool, fixtures help achieve consistent dimensional accuracy, even for complex geometries.
5.Adaptability to Different Workpieces
Modern honing fixtures are designed to handle various shapes and sizes of workpieces. Whether it's a cylinder bore, a fuel injector, or an aerospace component, the right fixture can adjust to the specific requirements of the job, ensuring consistent quality across different parts.
Types of Honing Fixtures
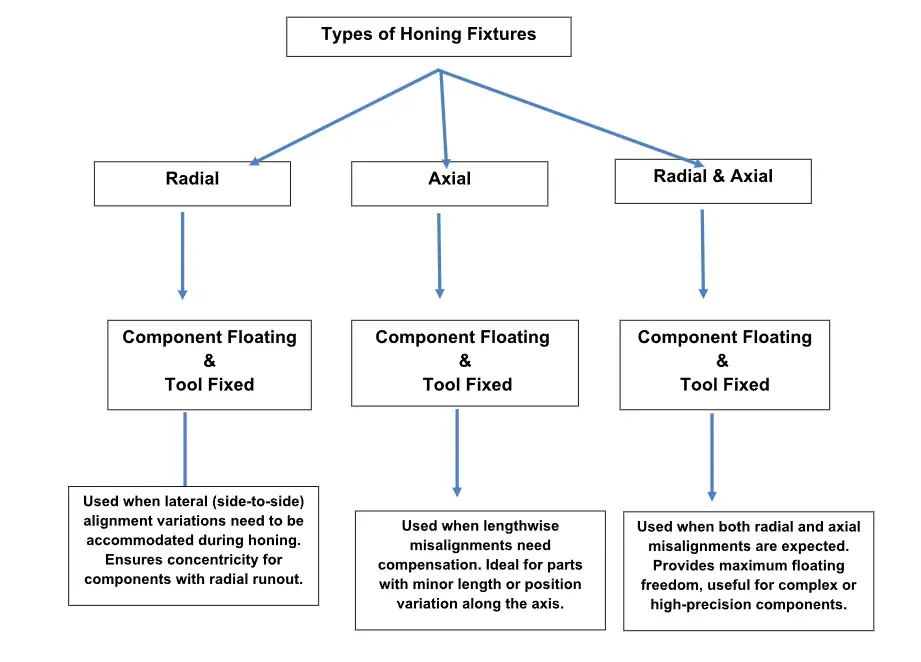
Radial Honing Fixtures
Radial fixtures hold the workpiece from the sides, allowing the honing tool to apply even pressure along the length of the bore. These fixtures are ideal for cylindrical components where uniform surface finish is critical.
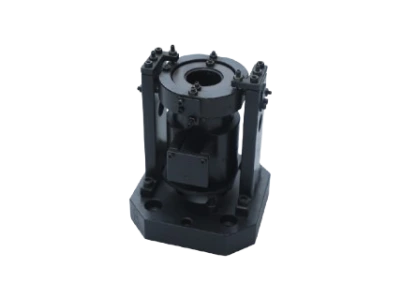
Role of Radial Fixtures in Honing
A radial fixture in honing is used to ensure proper alignment, stability and positioning of the component during the honing process. Its key purposes include:
Maintaining Roundness and Concentricity
- The fixture helps prevent ovality or out-of-round conditions by ensuring uniform pressure distribution
- It supports the workpiece radially, minimizing distortion during honing.
Enhance Stability
- Reduces vibrations that can affect the surface finish and accuracy.
- Ensures consistent contact between the honing tool and the bore surface.
Controlling Floating or Fixed Positioning
- Depending on the honing application, the component can be held rigidly or allowed to float radially to self-align with the honing tool.
- Floating radial fixtures allow minor self-corrections, improving bore alignment.
Improving Process Efficiency
- Reduces setup time by precisely positioning the component.
- Enhance repeatability, ensuring uniform results across multiple parts.
Axial Honing Fixtures
Axial fixtures hold the workpiece from the ends, providing stability during longitudinal honing. An axial floating fixture in honing is used to allow controlled movement of the component along the axis of the bore during the honing process. This type of fixture plays a crucial role in ensuring precision, especially in alignment and bore geometry corrections. It is often used for honing long, narrow components like engine cylinders.
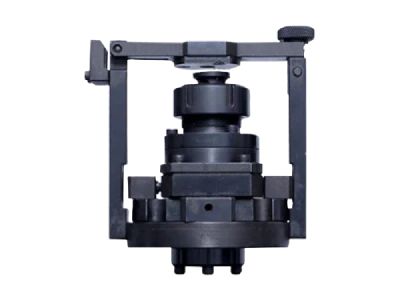
Function of Axial Floating Fixtures in Honing
1.Self – correction of Misalignment
If the component or honing tool is not perfectly aligned, axial floating allows minor adjustments, ensuring better alignment with the tool.
2.Improved Surface Finish and Roundness
- Axial floating ensures uniform contact between the honing stones and the bore surface, leading to consistent surface finish.
- Helps in maintaining roundness and straightness by reducing pressure variations.
3.Compensation for Tool or Component Movement
- If the honing tool has slight misalignment, axial floating allows the workpiece to adjust dynamically, preventing tool deflection.
- Useful in long bore honing, where maintaining straightness is critical.
4.Reducing Stress on the component
- Fixed holding of components may induce stress, leading to micro – distortions in the bore.
- Axial floating minimizes unnecessary force application, leading to better dimensional stability.
5.Application in Various Honing Setups
- Used cylinder honing, precision bore finishing and single pass honing where alignment errors can affect accuracy
- Beneficial in soft material honing where excess clamping pressure may deform the workpiece.
Radial & Axial Combined Fixtures
Combined fixtures provide both radial and axial support, ensuring maximum stability and control over the honing process. These fixtures are ideal for complex components requiring precise surface finishes and dimensional accuracy.
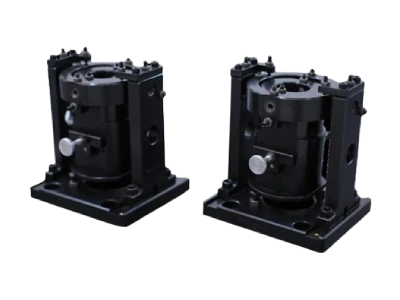
Significance of Radial and Axial Floating Fixtures in Honing
1. Self-Alignment of the workpiece
- Radial floating allows the workpiece to adjust laterally, ensuring even contact with the honing tool.
- Axial floating permits slight movement along the bore axis, reducing misalignment issues.
2. Enhanced Bore Geometry Control
- The fixture ensures better concentricity and cylindricity by compensating for minor inaccuracies in tool alignment or spindle runout.
- It is particularly beneficial when honing long bores or thin-walled components, where rigid clamping could distort the part.
3. Improved Surface Finish and Consistency
- Floating action ensures uniform pressure distribution of the honing stones.
- Reduces the risk of excessive stock removal on one side, leading to a more uniform finish.
4. Reduction of Workpiece Stress and Deformation
- Hard Clamping can introduce unwanted stresses, leading to micro distortions.
- A floating fixture minimizes these stresses, maintaining dimensional stability.
5. Application in Precision and Deformation
- Commonly used in automotive cylinder honing, hydraulic components, and aerospace precision bores.
- Beneficial for delicate materials like aluminium and thin-walled components where excessive clamping pressure could cause deformation.
Why Consistency Matters in Surface Quality
In industries like automotive, aerospace, marine, railway, power generation, renewable energy, oil & gas, and hydraulics, surface quality is directly linked to performance and reliability. Inconsistent surface finishes can lead to increased friction, poor sealing, and premature wear all of which can compromise the functionality of critical components.
By using a high-quality honing fixture, manufacturers can:
- Improve the lifespan of components
- Enhance performance by reducing friction and wear
- Ensure better sealing in hydraulic and pneumatic systems
- Meet industry standards for precision and surface finish
How to Choose the Right Honing Fixture
Choosing the right honing fixture depends on several factors:
Component Process Requirements
The selection of fixtures varies based on the specific honing process and the type of component being machined. Different processes may require different holding mechanisms to achieve optimal results.
Accuracy & Geometrical Tolerance
The choice of tools and fixtures depends on the required precision and geometric tolerances. High-precision components demand fixtures that provide superior stability and alignment.
Material Consideration
The material of the workpiece also influences fixture selection. Harder materials may require more robust fixtures with higher clamping force, while softer materials might need specialized fixtures to prevent deformation.
Tolerances
If tight tolerances are required, select a fixture that provides consistent pressure and alignment.
Production Volume
For high-volume production, automated or quick-change fixtures can reduce setup time and improve efficiency.
Type of Honing Machine
Ensure the fixture is compatible with the honing machine type (vertical, horizontal, single-pass, multi-pass).
Which Honing Fixture Best Suits Which Honing Machine
1. Vertical Honing Machine
Best-Suited Fixtures:
- Radial Fixtures – Ideal for holding cylindrical components vertically, ensuring even contact with the honing tool.
- Axial Fixtures – Provide stable support for long components, maintaining alignment during vertical honing.
- Radial & Axial Combined Fixtures – Ensure enhanced accuracy and stability for complex and irregular shapes.
Applications:
- Engine cylinder bores
- Hydraulic and pneumatic components
- Aerospace components
Sectors:
- Automotive – Engine blocks, brake cylinders
- Aerospace – Turbine housings, landing gear
- Oil & Gas – Valve seats, cylinder sleeves
- Hydraulics – Hydraulic cylinders, piston rings
2. Horizontal Honing Machine
Best-Suited Fixtures:
- Radial Fixtures – Provide side support, ensuring consistent pressure along the bore’s length.
- Axial Fixtures – Hold components securely at the ends, ideal for long and thin parts.
- Custom Fixtures – Designed for specific geometries or non-standard workpieces.
Applications:
- Transmission gears
- Hydraulic sleeves
- Fuel injector bodies
Sectors:
- Automotive – Transmission gears, brake rotors
- Aerospace – Fuel injector bodies, landing gear parts
- Oil & Gas – Valve bodies, pipeline components
- Hydraulics – Sleeves, control valves
3. Single Pass Honing Machine
Best-Suited Fixtures:
- Radial Fixtures – Ensure proper alignment and stability during high-speed single-pass honing.
- Axial Fixtures – Provide end-to-end support for better dimensional accuracy.
- Fixed Fixtures – Ideal for high-volume production where quick changeovers are required.
Applications:
- Brake cylinders
- Valve seats
- Turbocharger housing
Sectors:
- Automotive – Brake cylinders, turbochargers
- Aerospace – Valve seats, jet engine parts
- Hydraulics – Pump components, hydraulic pistons
4. Multi-Spindle Honing Machine
Best-Suited Fixtures:
- Radial & Axial Combined Fixtures – Provide maximum support and alignment for multiple spindles working simultaneously.
- Automated Fixtures – Enable faster loading and unloading for mass production.
- Flexible Fixtures – Adapt to different workpiece shapes and sizes without needing reconfiguration.
Applications:
- Cylinder liners
- Fuel injection components
- Hydraulic blocks
Sectors:
- Automotive – Cylinder liners, fuel injector bodies
- Aerospace – Landing gear, fuselage parts
- Oil & Gas – High-pressure cylinders, valves
- Hydraulics – Hydraulic blocks, control valves
5. Expansion Honing Machine
Best-Suited Fixtures:
- Radial Fixtures – Control the expansion pressure and maintain alignment during honing.
- Radial & Axial Combined Fixtures – Ensure enhanced control over complex geometries.
- Self-Centering Fixtures – Adjust automatically to maintain precise positioning.
Applications:
- Aerospace engine components
- Precision hydraulic cylinders
- High-performance automotive parts
Sectors:
- Automotive – Performance engine components, fuel injectors
- Aerospace – Turbine housings, landing gear components
- Oil & Gas – High-pressure cylinder sleeves, drilling components
- Hydraulics – Precision hydraulic cylinders, pumps
6. Manual Honing Machine
Best-Suited Fixtures:
- Simple Radial Fixtures – Provide basic alignment and support for manual operation.
- Custom Fixtures – Designed to fit specific components where manual adjustments are needed.
- Adjustable Fixtures – Allow flexibility for different component sizes and shapes.
Applications:
- Prototype components
- Low-volume production
- Custom-engineered parts
Sectors:
- Automotive – Custom engine parts, gear prototypes
- Aerospace – Experimental aircraft parts
- Oil & Gas – Custom pipeline components
- Hydraulics – Prototypes and low-volume production
Excellence in Honing Solutions
Honing fixtures are essential for achieving superior precision, uniformity, and efficiency in the honing process. A well-designed fixture ensures optimal alignment, stability, and repeatability, resulting in exceptional surface quality and dimensional accuracy.
Abhi Fine Products specializes in manufacturing high-performance, fully customized honing solutions with in-house production capabilities to ensure strict quality control. We produce a complete range of honing products including all types of honing machines, honing tools, fixtures, and accessories designed to meet specific customer requirements. With a strong global presence, we proudly deliver our expertly engineered solutions to customers around the world. Trust Abhi Fine Products to elevate your efficiency, accuracy, and overall machining excellence.
Tell us how can we assist you?
We are always happy to answer any questions!
Just fill in the form and we will get back to you.
© 2025 All rights reserved. Abhi Fine Products.
Designed & Developed by Appac Mediatech Pvt Ltd